According to the World Economic Forum data (2019), E-waste is considered the “fastest-growing waste stream in the world” with 44.7 million tonnes generated in 2016- equivalent to 4500 Eiffel towers. In 2018, an estimated 50 million tonnes of e-waste was reported, thus the name ‘tsunami of e-waste’ given by the UN. Its value is at least $62.5 billion annually.
Rapid changes in technology, changes in media (tapes, software, MP3), falling prices, and planned obsolescence have resulted in a fast-growing surplus of electronic waste around the globe. Technical solutions are available, but in most cases, a legal framework, a collection, logistics, and other services need to be implemented before a technical solution can be applied.
In our lab, we are providing both technical and policy solutions to the recycling, recover, and reuse of some of the E-waste with our advantages in fundamental science and technology, materials science and engineering, and circular economy.
Waste Printed Circuit Boards
Printed circuit boards (PCBs) represent one of the most complicated and valuable components in electric and electronic equipment (EEE). Waste PCBs (WPCBs) contain more than 40 kinds of metals with a wide and variable range of concentrations, such as environmentally harmful metals (e.g., Pb, Cr, As, Cd and Hg) and others of economic value (e.g., Cu, Sn, Au, Ag and Pd). Recovery of metals from WPCBs is of great importance for both environmental protection and resource re-utilization. Hydrometallurgy has been successfully used for metals recovery from waste printed circuit boards, due to its easily controlled process and high recovery rates at relatively low costs.
In our research, we focused on the revovery of base and precious metals in the waste printed circuit boards, where the following aspects were emphasized.
Novel leaching system, primarily leaching solutions, of both base metals and precious metals
WPCBs contain abundant metals composition, and efficient recovery of metals is the main goal of researchers. In view of the problems of current leaching systems, firstly, the response surface methodology (RSM) was used to optimize the experimental parameters of base metal (Sn, Pb, Cu) leaching system. And quadratic regression models were established to improve their leaching rates. Then, in response to the problems of the traditional gold leaching system CuSO4-Na2S2O3-NH3·H2O, a new efficient and eco-friendly leaching system was proposed to reduce the consumption of reagents, environmental pollution, and improve Au leaching rate. Finally, an efficient metals leaching system was obtained from WPCBs.
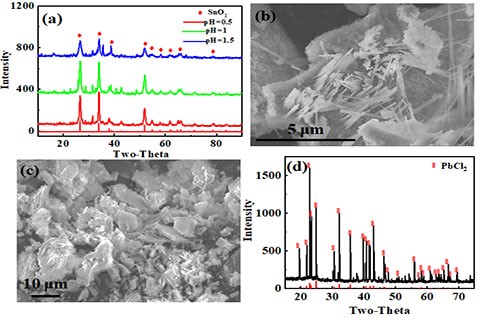
Leaching of base metals: (a) XRD patterns for SnO2; (b) SEM photo of SnO2 (10000); (c) SEM photo of SnO2 (5000); (d) XRD pattern for PbCl2.
Leaching kinetics and mechanisms of the system
According to the studies of experimental parameters of base metals leaching system, the leaching mechanism of base metals is still unclear. In order to further understand the leaching mechanisms of base metals, the leaching kinetics of base metals (Sn, Pb, Cu) were studied, and kinetic equations were established integrating various experimental parameters. The leaching processes of Sn and Pb conform to the shrinking core model (SCD), and are controlled by mixed reaction and diffusion reaction, respectively. The leaching process of Cu conforms to the Avrami model.
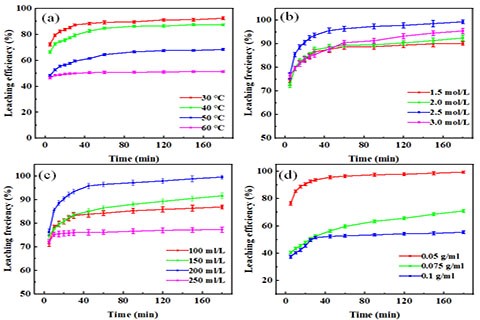
The effect of variables on the copper leaching efficiency ((a) Temperature; (b) H2SO4 concentration; (c) H2O2 concentration; (d) Solid-liquid ratio).
A complete recycling flowsheet of metals from WPCBs
After leaching of metals with different leaching systems, the metals in the leaching solution need to be recovered. Tin and lead, copper and gold were leached using hydrochloric acid (HCl), sulfuric acid-hydrogen peroxide (H2SO4-H2O2) and thiosulfate, respectively. According to the characteristics of different leaching systems, precipitation method, electrodeposition and solvent extraction were applied to recover metals from leaching solutions obtaining lead chloride (PbCl2), tin dioxide (SnO2), cathode copper (Cu) and gold (Au). Finally, a stepwise metal recovery system was established.
Waste Emameled Wires
With the development and application of information technology and artificial intelligence, more and more service terminals are used in banking services, car charging and other scenarios. At the same time, the speed of equipment elimination is accelerating due to technology upgrading and function enhancement. The recycling technology of metal parts and circuit boards in the main disassembly products of waste service terminals is relatively mature, but the recycling technology of enameled wire in it is not, and there is a serious risk of secondary pollution in the recycling process. Based on the continuous pyrolysis recovery and utilization technology of waste enameled wire, we have investigated the pyrolysis mechanism of organic coating and the influence of key parameters on the pyrolysis to achieve complete carbonization of organic coatings on enameled wire. Our main research efforts include: (1) Pyrolysis of organic coatings under the control of temperature and atmosphere. The influencing mechanisms of different temperatures and atmosphere on solid and gas pyrolysis of organic coatings are analyzed to establish theoretical system of pyrolysis. (2) High-temperature pyrolysis process optimization. Through calculation and simulation, the comprehensive balance management strategy of pyrolysis, material and energy consumption are optimized to carry out the overall engineering process design and technical evaluation and verification, so as to propose a reasonable continuous pyrolysis process design scheme.
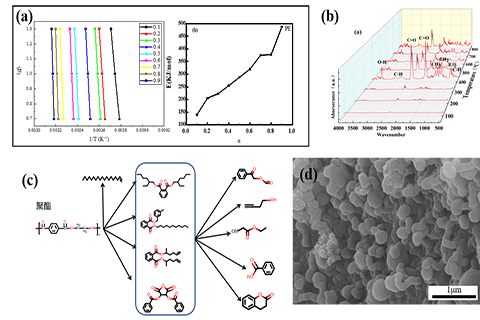
(a) Conversion rate and activation energy of enameled polyester wire;(b) TG-FTIR of polyester enameled wire;(c) Pyrolysis gas product conversion process of organic coating on polyester enameled wire;(d) Morphology of solid products after pyrolysis of polyester enameled wire.
Representative Publications:
郝娟娟, 王乙舒, 吴玉峰, 郭福. 废线路板非金属材料回收利用技术现状与展望[J]. 材料导报, 2021, 35(7): 07001-07012.
Xia Z D, Xie X Q, Shi Y W, et al. Recycling cobalt from spent lithium ion battery[J]. Frontiers of Materials Science in China, 2008, 2(003): 281-285.
Hao J J, Wang Y S, Wu Y F, Guo F. Metal recovery from waste printed circuit boards: A review for current status and perspectives[J]. Resources, Conservation and Recycling, 2020, 157: 104787.